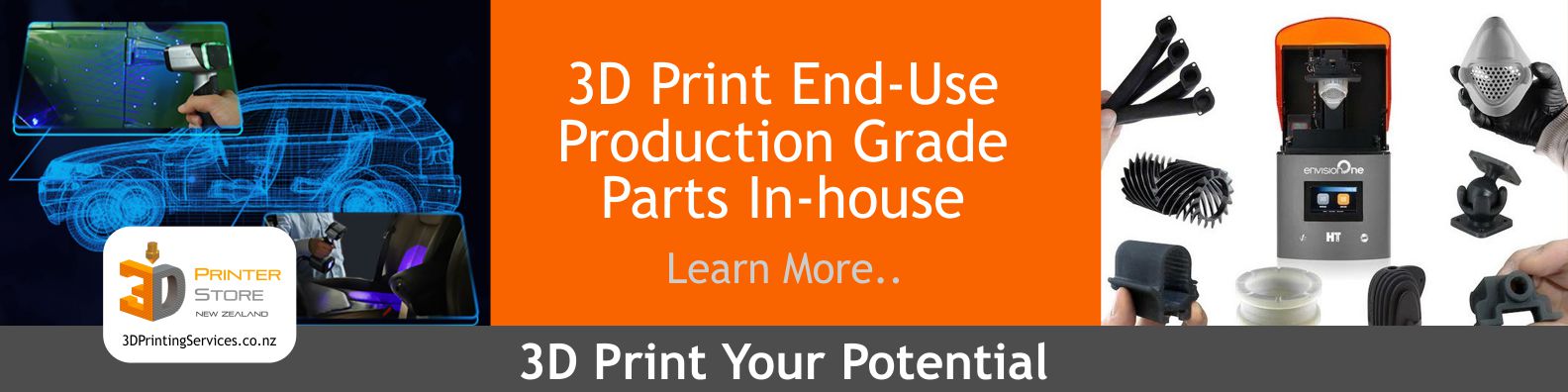
Whether its Prototypes or Customer Facing products, Production Quality 3D Prints are here..
A vast range of 3D printers & materials are now available across various 3D printing technologies that manufacture parts which perform to the levels you would expect from a factory quality part.
With the capability to use everything from Carbon Fiber reinforced Nylon through to PEEK Thermoplastics, and the latest generation Liquid Resins that create Injection Moulding surface quality parts at high speeds, anything can now be 3D Printed with today’s Additive Manufacturing technologies.
To make things even more interesting, there are many casting & sintering material options available, allowing you to manufacture complex metal parts at a fraction of the cost & time it would take to make them with conventional machining processes, without having to invest in million dollar metal 3d printers.
What are the benfits of having a high quality 3D Printer in-house ?
3D Printing has long been looked at as fundametnally a protyping technology, good for maybe a few protypes ini the internal design phase, & often not even fit for final customer facing prototypes of parts that were going to be injection moulded.
For parts which were not end custoemr facing, there were still cases where 3d printed prototype parts would just not perform in real world testing, often cracking due to common FDM 3d prints being isotropic (weaker in the Z axi due to poor inter-layer adhesion of 3d printed parts made in layers).
All of this is starting to change rapidly, with technological improvements in mechatronics, but more importantly, in material chemistry.
The machinery is also further improved to be able to handle materials that can be more Anistropic (equally strong in all axi despite being made in layers).
Why is this a game changer for Product Design, Engineering, & Manfacturing sectors ?
Because it opens up workflows, that we could never considered earlier..
For eg, Small Batch Production runs of parts using a 3d printer.
Having confidence that AM is actually usable, we can then follow a DFAM (Design for Additive Manufacturing) process when creating parts from the very start.
Firstly, this often reduces material use & weight, which is important when every business if trying its best to reduce carbon footprints, improve the circular economy, & wants to play a part in the Eco Green movement.
And on top of this, there is a economic advantage.
In-house 3D Printers which make end use parts allow you to quickly make small batch production runs that can actually be sent to market.
This is an instant cashflow, & a competitive advantage in itself.
You now start getting critical feedback from customers, which allows you to fine tune designs without any tooling costs.
And producing on demand removes the need to carry stock.
The global shipping & logistics scene is no surprise, with factory backlogs in raw material supply, often it is easier to acquire 3D Printer consumables, make the products in small batches, & fulfull customer orders.
Contact us today to check how our 3D Printers & Material Options can accelerate your Product Design & Manufacturing processes.
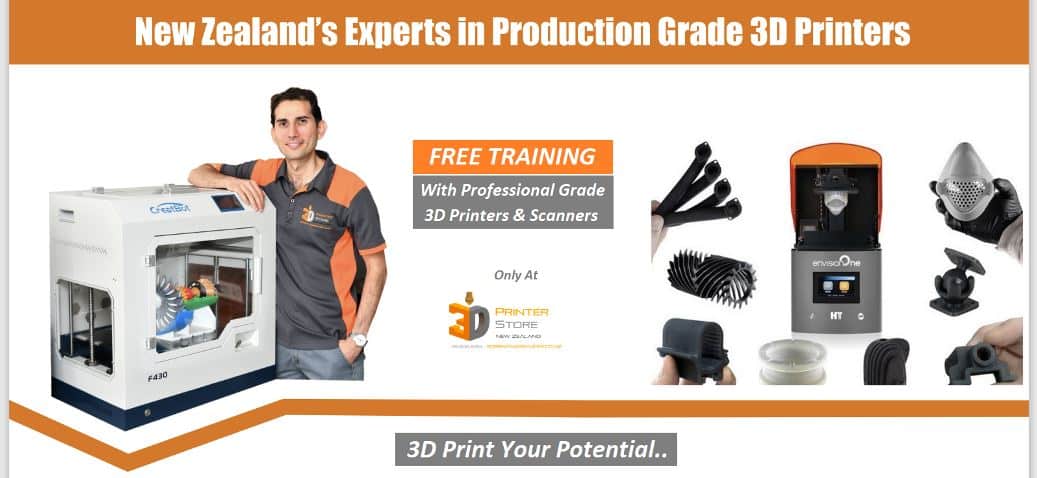
What is the advantage of DFAM?
DFAM often reduces part complexity, rather than complicating it because true DFAM starts with inproving the form, fit & function of the part.
It allows you to manufacture any part in an efficient way using 3D Printing Technology.
But in the past, we would not always consider this option, because it would not make a part that was truly ‘sellable’.
And for that reason, we would not be able to prototype effectively, because the parts were always going to be moulded or machined.
Why bother creating a DFAM prototype when the final product can be adversely impacted by DFAM.
This would lead to the dilemma of 3d printing a non-dfam part, only as a weak, odd looking unusabble prototype, for a final technology that was different.
Why would we have honestly Designed for Additive Manufacturing, if we knew for well that we were just not going to adopt AM later on!
There was no point for many Small-Medium businesses, or for most Small batch Production roll outs, unless they were extremely Niche one-off products.
It may seem that DFAM is just about hollowing everything out & making complicated grid structures, internal channels, & inlets.
This is not an accurate representation of DFAM.
DFAM allows us to use high quality 3d printers with good quality materials to Additively Manufacture parts that would never have made the cut before as a 3D Printed part.
3D Printing End-use professional grade parts is now very real, & we have implemented these workflows for businesses of all shapes & sizes.